ストーリー
Ⅷ. Kyushu's Pottery and Ceramics: Evolving traditions of production
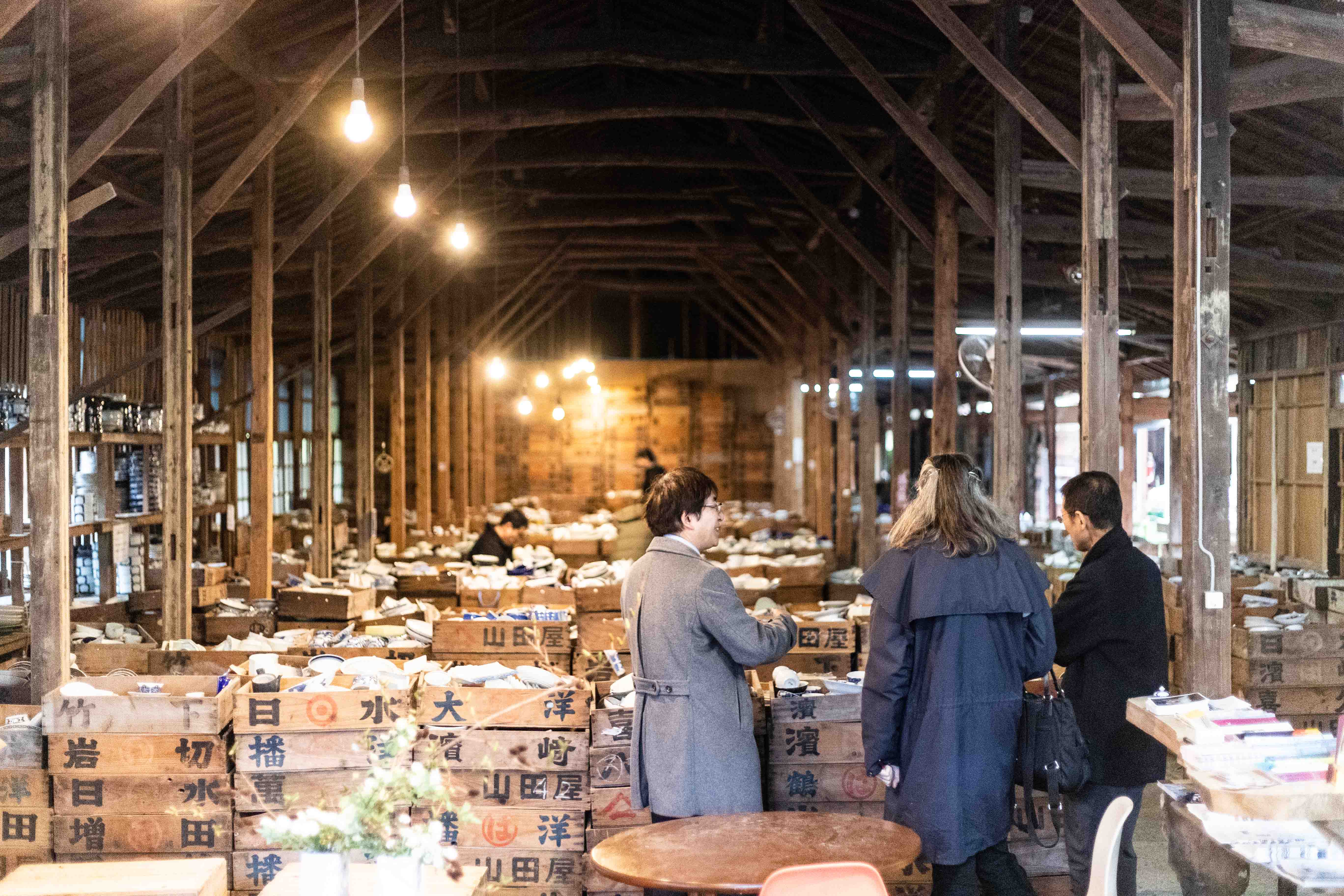
By:
Vicki L. Beyer
As noted earlier, Kyushu has
centuries, if not millennia, of history relating to pottery and ceramics.
Indeed, one of Kyushu's major exports to the West during the Edo Period, when
most of Japan was closed to the outside world, was porcelain products. The
pottery villages producing these wares grew to become among the best known in
Japan. Still today, they continue to practice their craft and are delightful
places to visit.
Kyushu's modern pottery production
dates from the end of the 16th century when warlord Toyotomi Hideyoshi
(1537-1598) returned from campaigning in Korea with a group of knowledgeable
Korean potters. Once in Japan, they went on to identify a region in modern Saga
Prefecture as having the best clay for producing ceramics. Most notably, a type
of clay mineral known as kaolin, essential to the production of porcelain, can
be found in this area.
Pottery and ceramics, of course,
were in production even before potters in Kyushu learned to make porcelain. The
earliest products were bisque-fired earthenware, including pots for storage and
cooking, as well as figurines used in religious (especially death-related)
observances.
Kyushu potters began to produce
stoneware when the technologically-advanced "climbing kiln" was
introduced to Japan from China via Korea in the fifth century. The climbing
kiln is a multi-chambered kiln constructed on a hillside, with the successive
chambers "climbing" the hill.
The fire heating the kiln is stoked from the bottom, allowing the heat
to rise upward through each chamber before escaping at the top. This structure
efficiently provides proper heat distribution at higher temperatures than had
previously been possible. Many potters around the world, including in Kyushu,
who prefer to wood-fire their pottery, continue to use climbing kilns today.
One of the oldest surviving climbing kiln sites in Japan, believed to date back
to 1734, is located in Karatsu and is today designated as a historical site.
Not long after the introduction of
improved kiln technology, glazes also appeared. Natural ash glazes were likely
the first to come into use, simply a by-product of the firing process. By the
6th or 7th century, sancai — glazing
in three colors: green, brown, and cream — was introduced from China. From
there, Japanese potters could begin to experiment and expand glaze technology
for themselves.
Nonetheless, the great leap forward
in pottery production came with the discovery of kaolin. Chinese and Korean
craftsmen had already been producing porcelain but Japan had lacked both the
key ingredient of kaolin and the technical know-how. Legend has it that kaolin
was found in 1616 in the village of Arita by a Korean potter named Kanagae
Sambee (also known as Yi Sam-pyeong). The now-defunct site on the outskirts of
Arita, locally known as Izumiyama Quarry, can still be viewed by visitors.
Kanagae is honored with a monument at nearby Sueyama Shrine, Arita's shrine to
the god of ceramics. The hilltop shrine (also referred to as Tozan Shrine)
further honors its god with ceramic lion dog statues guarding its ceramic torii
shrine gate. Even its ema votive
plaques are ceramic, instead of the usual pine wood.
Arita is still regarded as one of
the leading pottery villages of Kyushu. It is one of eight pottery villages of
the former Hizen Province: Arita, Imari, Karatsu, Takeo, and Ureshino in modern
Saga Prefecture and Hasami, Hirado, and Sasebo in modern Nagasaki Prefecture.
Generally (although not always), the pottery, whether stoneware or porcelain,
of each village, is identified by its point of origin, combined with the word yaki, meaning "ware." For
example, pottery from the town of Arita is known as Arita-yaki, while this of Karatsu is Karatsu-yaki.
During the feudal times, artisans
and craftsmen served at the pleasure of their feudal lord. They were
essentially tied to their village and their craft, unable to move or change
professions without the consent of their lord. Nearly everyone in the village
was involved in some aspect of pottery production, which is an intricate
process requiring substantial infrastructure and support. In addition to
potters, there were also people to mine and prepare the clay, foresters to
ensure sufficient wood for the kilns, chemists to prepare glazes, and painters
to add the decorations. The principal work of each pottery village was to
produce pieces for use by the feudal lord or his retainers, including items for
everyday use by the common folk subject to the particular lord.
Different pottery villages developed
different styles of pottery, some specializing more in stoneware and others in
porcelain. In some cases, the nature of the locally available clay dictated the
type of pottery produced. There are also certain types of glazes particularly
associated with certain villages. This
is not to say there aren't variations and cross-over, but there are certain
general patterns.
Karatsu-yaki
The coastal castle town of Karatsu
has a number of kilns and is known for its stoneware produced in earth tones.
Modern pottery production here dates to 1596, even before the discovery of
kaolin that began porcelain production in Kyushu, giving a solid reason for
Karatsu to claim to be the origin point of Kyushu ceramics.
During the Edo Period, when everyone
worked for the feudal lord, potters didn't necessarily have much creative
freedom. The lord indicated what he wanted and it was the potters' job to
produce it. The order may have been for everyday
items for use in Karatsu's castle or by the townspeople, or it may have been a
specialty item — such as a gift for the shogun, for example. What the potters
lacked in creative freedom they made up for with their high level of technical
skill.
One particular feature of the
Karatsu-yaki stoneware is how comfortable it is. The sizes and shapes of pieces
seem to fit naturally into one's hands. The ash-based glazes also have a
natural look, possibly enhanced by the fact that Karatsu's local clay has a high
iron content. The decorations etched or painted onto the glaze are typically
simple, complementing the shape and color of the final craft. Patterns on
everyday dishes are designed to be revealed as the food served on them is
eaten, enhancing the pleasure of the meal in a way rarely conceived of in
Western meals.
Karatsu-yaki implements for
traditional Japanese tea ceremony are especially prized. One place to examine
some of these pieces is at the kiln of Nakazato Taroemon, a 14th generation
potter deriving from a family that has long specialized in teaware. The
Nakazato kiln, located in the Choda district of Karatsu, is also known as o-chawan-kama (honorable tea bowl kiln).
To date, Nakazato potters continue to use their three wood-fired climbing kilns,
maintaining that the ash and smoke involved in firing this way form an integral
part of the ultimate glaze and finish of their work.
Since all Nakazato potters take the
given name of Taroemon, it's simplest to refer to them by their generational
number — even the current Nakazato Taroemon speaks of his ancestors and their
work that way.
Notwithstanding the strong desire to
preserve and protect traditional firing and other methods of production,
Taroemon number 14 insists that it is also essential to leave room for
creativity. He says that he wants to take the craft in his own direction, rather
than just repeating what came before. Indeed, to hear him talk, it seems that
the Nakazato potters have always innovated and stretched themselves, trying out
new designs and styles. Each has also played to his particular interests and
artistic strengths. For example, number 12 was not only a skilled potter but
also a fine sculptor. A large ceramic dharma figure made by him graces a garden
inside the kiln and studio complex.
Taroemon number 14 is both a
creative and technical innovator who is developing a method of dissipating the
smoke leaving the kilns so that it does not bother his neighbors. This wasn't a
problem when the Nakazatos built their first kiln here in 1734, but the city
has grown up around them over time. Number 14, however, doesn't let innovation
crowd out tried and true methods. He says when he's working on art pieces, such
as tea ceremony ware, he prefers to use a 200-year-old foot-operated wheel. He
says it enables him to better feel what he's creating. Indeed, Taroemon number
14 believes it is the technical skills of Karatsu potters that makes
Karatsu-yaki so special.
The Nakazato kiln is welcoming to
visitors, with a shop and galleries where visitors can see displays of a number
of modern and antique works to come out of their kilns. Opening in March 2020,
a gallery in the renovated minka
(traditional style) home of Taroemon number 11 includes works of at least four
generations of Nakazato potters. The gallery includes an adjacent fireproof
warehouse. Look closely at some of the older pieces in the warehouse to see
examples of kintsugi (golden
joinery), the practice of using gold-dusted lacquer to repair broken pieces
considered too fine to discard.
Across the road from this gallery is
the kiln's original gallery and shop, a chance to gain further appreciation of
the craft. The items in the original gallery are among the best works of number
14, and his father, number 13, items made in a range of styles and glazes.
Again, generational differences in style are also apparent. Number 13 was
especially fond of decorating his larger pieces with a swathe of turquoise
glaze and images of fish. Number 14 tells tales on his father, revealing that
his father would use a dead fish as his model. (Number 14 has some decorative
carp in a tank in his workshop and uses those as his live models when
decorating using fish.)
The Nakazato kiln produces a wide
variety of dishes for everyday use as well as its artistic pieces, usually by
subordinate potters working in the studio. This commercialization was a method
for survival that most Kyushu potters had to adopt at the time of the Meiji
Restoration (1868) when the loss of a feudal lord meant the loss of a steady
employer for the potters.
For a chance to see more
Karatsu-yaki, particularly tableware, visit the Furusato Hall Arpino near JR
Karatsu Station. They have an exhibition about the production of Karatsu-yaki
and display Karatsu-yaki from a number of the local kilns.
Takeo Kokaratsu-yaki
The Takeo pottery village, in the
southern part of Saga Prefecture, claims to be the predecessor of Karatsu-yaki,
since it, too, can trace its history back to a Korean potter brought to Kyushu
by Ienobu Goto, a feudal lord fighting on behalf of Toyotomi Hideyoshi. Similar
to Karatsu-yaki and often referred to as Takeo Kokaratsu-yaki (Kokaratsu means
"old Karatsu"), this stoneware is known for its simplicity, warmth
and earth tones. This style was said to be the most common for everyday items
used by the common people of Hizen.
Nabeshima-yaki
In 1607, Ienobu Goto ceded his power
as a feudal lord to the Nabeshima family, whose name is now associated with one
of Kyushu's most elegant porcelain. Nabeshima-yaki began to be produced in the
late 17th century and continued in production until the late 19th century. It
is extremely high-quality porcelain produced under the patronage of the
Nabeshima feudal lords for their own use but also for them to use as gifts of
tribute to the Tokugawa shoguns and other high-ranking officials, or even for the
Emperor.
Most Nabeshima-yaki was produced in
Okawachiyama, a secluded village not far from Imari and Arita. Nabeshima pieces
show an extraordinarily high level of sophistication. Among the distinguishing
features of Nabeshima-yaki are the dishes' shapes and sizes and the colors and
patterns of the glazes used. Chinese-style lion-dog figurines, often glazed in
celadon, were a particular Nabeshima specialty.
Delicate application of overglazes
by highly skilled artisans produced unique variations in tone and color. The
designs decorating Nabeshima pieces tended to be more Japanese than Chinese in
style, simple asymmetrical depictions of flowers or geometric patterns. This
deviation from standard practice with pottery must have seemed revolutionary at
the time. Anything imperfect or flawed was destroyed in an effort to maintain
the highest quality standards. The Nabeshima lords took a close interest in
supervising the work of the potters, perhaps to ensure the high quality of
Nabeshima-yaki. They were also extremely secretive about the production methods
that resulted in such high quality pieces. The seclusion of Okawachiyama helped
preserve their secrets.
Visitors can get a sense of this by
visiting the Nabeshima Domain Kiln Park, which has a reproduction checkpoint/guardhouse,
old kilns, and even old potter's huts. Stroll the narrow streets of this
hillside village and drop in to some of the shops selling locally-produced
porcelains to absorb more of the atmosphere.
Arita-yaki and the Imari ware brand
As mentioned above, the kaolin
necessary to make porcelain was first found in Arita in 1616. Japan's upper classes were already familiar
with porcelain, which had been introduced from China. But there was a strong desire to produce
porcelain domestically, which was exacerbated by the limited availability of
imports due to political unrest in China in the 17th century.
The Chinese situation produced not
only domestic demand for Kyushu's porcelain but also international demand – The
Dutch traders of Nagasaki began to place orders as well. The initial requests
were for dishes in shapes familiar to the Japanese, for use in other parts of
Asia that the Dutch were trading with. In producing these items, Arita's
potters also emulated the blue on white glazes of the original Chinese
products, often copying the Chinese motifs as well.
It wasn't long before the Dutch
decided that they could export Kyushu-made porcelain to Europe as well, given
that products that would appeal to the European market were produced. This was
the beginning of the Imari ware. Imari ware is the name by which Kyushu's
export-grade porcelain came to be known in the West because Imari is the name
of the port from which the goods were shipped. Imari ware came from several
different pottery villages of Hizen, although, generally, Arita is considered
to be the largest and most prolific. Dutch traders worked closely with potters
to introduce them to styles and designs that would appeal to the European
market. The items produced for export during the Edo Period, now mostly museum
pieces, have come to be known as "Ko-Imari" (old Imari).
Export pieces tended to be larger
than those for domestic use, including lidded dishes of various sizes, plates
larger and flatter than the Japanese of that time would use, stemmed goblets,
and serving bowls and platters. The shapes were also unusual by domestic
Japanese standards. Rather than round, they would be oblong, square, or
octagonal. Sometimes the rims would be fluted or scalloped. In particular
demand were ornamental pieces, including vases and decorative jars (sometimes
nearly as tall as a person), as were figurines, both large and small. Those
were typically used to adorn European homes and castles.
Not only the shapes but also the
decoration and glazes of export pieces tended to be different. While the Japanese usually preferred simple
asymmetrical designs, European taste ran to elaborate decoration, eventually in
multiple colors. This required hand-painting overglazes and multiple firings
which produced "enameled" pieces known as Kakiemon, taking the name
from the 17th-century potter who first developed this style of decoration.
Another popular form of decoration
for Imari ware was kinrande, meaning
gold brocade. Kinrande porcelains are finished with gold decoration, carefully
hand-painted onto the piece at the end of the glazing process. Kinrande pieces
are usually elaborately decorated on both sides, often with lush floral or
geometric images as well as animals and fish, mythical creatures, and people
from various walks of life. They can be studied as closely as any antique
scroll to reveal exquisite detail.
In the 19th century, European
exports dwindled, but the domestic market expanded. Perhaps, thanks to the rise
of a wealthy merchant class, the pottery of the greater Imari area became
popular across Japan, appearing in both restaurants and private homes. The
ever-adaptable Arita potters quickly modified motifs and colors to suit the
changing market.
Even today, the blue on white glaze
that gave Arita its start back in the 17th century is regarded as the signature
glaze color of Arita. Some argue that it is the standard for determining
whether a piece deserves to be referred to as Arita-yaki. At the same time, red
accents and other colors are not precluded and also remain popular, with new
glaze colors coming on line all the time.
According to Takanobu Tokunaga,
fifth-generation proprietor of Arita's Kouraku Kiln, there are three key
elements to Arita-yaki: the clay, the kiln, and the glaze. Tokunaga adds that
Arita's clay is ideally suited to porcelain production, requiring little mixing
or alteration. He goes on to explain that during the Edo Period, when pottery
villages essentially belonged to their feudal lord, being a potter native to
Arita was also essential. In modern days, that has changed, and many potters —
both Japanese and non-Japanese — come to Arita in search of inspiration and
skill development. One could say that Arita is a Mecca for devoted potters.
Kouraku Kiln has an "artist in
residence" program that particularly welcomes these newcomers. Tokunaga believes their input can inspire
local craftspersons to new designs and ideas. According to Tokunaga, this kind
of evolution of the craft is essential to the kiln's continuation. Among the
new features recently introduced at Kouraku are footed serving plates with the
foot attached by a strong magnet, so the plate can be disassembled for easier
stacking and storage. Dishes with glaze even on the base (which traditionally
has not been glazed) are popular with hostesses worried about scratching their
furniture. At the same time, Kouraku Kiln continues to produce popular items,
like the bird-shaped soy sauce dispenser designed by Tokunaga's father about 35
years ago. As Tokunaga says, "being innovative doesn't mean we have to get
rid of things that are working."
As one of the largest kilns in Arita
(they have four large gas-fired kilns on-site), Kouraku Kiln is able to engage
in all steps of the production process on-site. They use molds for many of
their pieces, but these must be replaced after 100 uses, requiring lots of
redundancy in their work.
Kouraku Kiln welcomes visitors to
its facilities, nestled on a wooded hillside. Visitors can apply a decal or paint
glaze onto a dish in their workshop and have it sent to their address after
being fired. Another fun activity is their "Treasure Hunt." Visitors
can pay 5,000 or 10,000 yen for a shopping basket and wander through a
warehouse stuffed with boxes of odd pieces, picking out the ones they want
until the basket is full. One reason this is possible is that the kiln always
over-produces when filling an order, as there is inevitable breakage. They
inevitably wind up with "extra" pieces and this Treasure Hunt is one
way to find good homes for them.
Arita is a relatively compact and
inviting town. Visitors can wander its pretty streets, ducking in and out of
boutiques, galleries and studios and soaking up the creative atmosphere. There
are a number of small museums and, like Kouraku Kiln, some kilns offer the
hands-on experience of painting glaze onto your own dish. In the oldest part of
the town, many potters' studios stand behind attractive high walls made of old
kiln bricks and broken pieces of pottery, the perfect form of recycling for
this pottery center.
To gain an in-depth understanding of
the history and complexity of Arita-yaki and Imari ware, be sure to visit The
Kyushu Ceramic Museum. The museum has a vast collection of Imari ware,
especially Ko-Imari, as well as more contemporary pieces. Its exhibits are
arranged to provide visitors with the history of pottery in Kyushu and an
overview of production, and then moves forward in time with displays of
significant pieces in various styles and from multiple kilns.
Another Arita attraction focusing
primarily on ceramics is the Arita Porcelain Park on the outskirts of town.
This is a kind of theme park dedicated to ceramics and includes a reproduction
of a famous climbing kiln and pottery lessons. It also has a museum with an
extensive collection of porcelains – both Japanese and European – housed in a
reproduction of the baroque-style Zwinger palace in Dresden, Germany.
Hasami-yaki
The village of Hasami lies south of
Arita, across the border into Nagasaki Prefecture. It, too, boasts four
centuries of pottery tradition, producing both stoneware and, later, porcelain
entirely by hand, resulting in rare and prized works. One of the signature
features of Hasami-yaki is its translucent white glaze and the fine lines of
delicate patterns in the overglaze. Icy blue-white celadon glazes are also
common on Hasami-yaki. The translucence of the porcelain is a function of the
fine, white kaolin used, which is mined in Amakusa.
One of Hasami's most famous products
during the Edo Period was "compra" bottles, large white bottles for
sake. These bottles are sometimes brought up from centuries-old shipwrecks,
still containing alcohol. Another signature Hasami-style is the graceful wickerwork
designs that are said to be produced only in Hasami. Everyday tableware made in
Hasami kilns, with its timeless style and moderate prices, has long been
favored as well.
The potters of Hasami have evolved
and innovated by working to create break-resistant tableware, a kind of
reinforced porcelain. This is particularly popular for school cafeterias. For a
time, at least, the famed Yoshinoya beef bowl was also commonly served in
Hasami-yaki bowls, possibly similarly break-resistant.
Like Arita, Hasami also has a
ceramics park. Known as "Yakimono Park," it features reproductions of
a dozen different kilns from around the world and across time.
Onta-yaki
Saga and Nagasaki are not the only
places in Kyushu with a pottery tradition. In Oita Prefecture, the tiny
mountain village of Onta has more than two centuries of history producing
stoneware in the folkcraft tradition. Its dishes are glazed in natural earth
tones, largely decorated by small lines etched into the surface of the pieces.
Most of the villagers of Onta are
involved in pottery production, working in family-owned studios passed from
father to son and sharing a wood-fired kiln that belongs to the village. As the
texture of clay needs to be just right for pottery production, the villages have
devised a river-powered mechanism for beating the clay to the desired
consistency. Visitors report that the thump of the mortars beating the clay is
a particular sound to be cherished when visiting Onta.
Onta enjoyed a surge of domestic and
international popularity when it was lauded by the mingei folk art movement for
its preservation of traditional production methods and styles.
Fukuoka's pottery
Another pottery village identified
by the mingei folk art movement was Fukuoka's Koishiwara. Koishiwara-yaki is characterized by its
brown and other earth-tone glazes and simple etched patterns. The pieces tend
to be designed for everyday use, and styles have evolved with Japanese eating
habits.
One particular feature of
Koishiwara-yaki is that it is "slipware." That is, before a piece is
fired, it is decorated by being dipped in or painted with slip, a kind of clay
soup containing various minerals, instead of glaze. This ancient style of
pottery decoration is one reason Koishiwara-yaki is associated with the mingei
folk art movement.
Hoshino village is another place
where pottery was produced for the feudal lord during the Edo Period. Because
the village was located in the Yame area, which is famous for tea production,
many Hoshino-yaki pieces were designed for storing, making, or drinking tea.
The earthenware was known for its dark reddish-brown glazes.
Unfortunately, the industry did not
survive industrialization, and pottery production died out before the end of
the 19th century. It was, however, revived in the 1960s and there are now
several artisan potters at work in Hoshino, reviving the craft and the natural
and dark glazes it was once known for.
Satsuma-yaki
Satsuma-yaki is produced in
Kagoshima Prefecture, which was formerly known as Satsuma. Throughout history, Kagoshima has also been a
gateway city for Kyushu and it, too, brought in Korean potters in the late 16th
century.
There are two principal types of
Satsuma-yaki porcelains: Shiromon
(white) and Kuromon (black). Shiromon
is a rich ivory glaze decorated with patterns of plants or animals in primary
colors with gold accents, often referred to as brocade. Shiromon has a lustrous
finish that exudes elegance.
The best pieces always belonged to
the Shimazu family, who were the lords of Satsuma. As the Shimazu lords became
increasingly involved in Japan's diplomatic efforts overseas, they often used
superior Shiromon pieces of Satsuma-yaki as gifts to overseas dignitaries and
royalty. During this period, when European demand for Japanese porcelain was
otherwise waning, exports of Satsuma-yaki, which had been displayed at the 1867
Paris Exposition, were high. One place to see examples of Shiromon is at
Sengan-en, the historical villa of the Shimazu family.
Kuromon, on the other hand, is a
luminous black, with little additional decoration. The color comes from
iron-rich volcanic ash used in the glaze. Kuromon pieces tended to be designed
for everyday use, giving them a universal appeal.
One of the original production
centers for Satsuma-yaki is the Miyama neighborhood of Hioki city. Visitors can still see a kiln operated by the
15th generation of the Chin family brought from Korea in the 16th century. At
the nearby Miyama Toyukan, a pottery gallery/studio, visitors can have the
opportunity to throw a pot on a wheel or dab a bit of glaze on a dish.
Pottery of Amakusa
Although Saga Prefecture is famous
as the place where kaolin was first found in Kyushu, today, 80% of Japan's
kaolin comes from Kumamoto's Amakusa Islands. It is a particularly fine, white
stone. Amakusa's pottery tradition began in the mid-18th century when a local
lord, realizing his peasants were unable to survive on farming alone, devised a
system of pottery production that could be done on a "part-time"
basis in the "off" season. The system thrived, as did pottery
production in Amakusa.
In particular, the Ueda family of
the west coast village of Takahama began to produce porcelains for Dutch
traders to export, leading to a substantial boon to the local economy. They
developed their skill in export-quality goods by importing a potter from Hizen,
who helped develop designs and patterns that would appeal to the Western
market. Based on Western expectations, they began by producing dishes glazed in
blue on white, often adorned with patterns originating from China. Over time,
as in Arita, floral designs red accents also became popular.
The old Ueda family's home and
garden, as well as a small museum containing exhibits on the kiln's history,
are located near the current kiln. The museum features many fine antique
pieces, dating back to the 1770s when production for export began. Since the
Takahama kiln made both products for export and products for domestic use,
examples of both are on display. An explanation notes that generally, the
designs of export items were not suitable for Japanese use and vice versa.
As also happened in other areas,
after the Meiji Restoration in the late 19th century, the kiln had to cease
operation. But a small Takahama-yaki kiln re-opened in 1952 and continues to
produce today, using many of the kiln's traditional designs and patterns.
One particularly distinctive motif
developed by the earlier Takahama kiln is called Mirumon. It looks like a clump
of coral or a spray of seaweed in blue glaze on the white dish. While the
original Mirumon dishes were produced in the traditional glaze color, in these
modern times, blue is sometimes replaced with yellow or red. The delicate white
dishes adorned with just a splash of colorful pattern are translucent and
practically glow when held up to the light.
Takahama kiln may be particularly
historic, but there are currently a number of active potters and kilns across
Amakusa's Shimoshima. One of the largest is the Maruo Kiln, which started
production in 1845 and takes its name from the district where it was located.
Now operated by the fifth generation of the Kanazawa family, three brothers,
the kiln maintains a large studio in Amakusa city. All three brothers, and
their mother, are potters, each designing their own distinctive wares and
producing them with the assistance of two other potters. Consequently,
Maruo-yaki consists of both stoneware and porcelain.
One particularly exciting feature of
Maruo-yaki is that each piece is handmade. As no molds are used in the making,
no two pieces are alike, even if at first glance they may appear to be. The
"daily ware" dishes have a natural look and feel that one can use for
years and never tire of.
Maruo-yaki has a large, airy
shop/gallery that invites visitors to browse, and the volume and variety means
this could take hours. At the far end of the shop is a small coffee bar with
indoor and outdoor seating. Purchase a piece of Maruo-yaki and get a
complimentary cup of coffee made with local beans and served in your choice of
a Maruo-yaki cup.
Annual Pottery Fairs
Various pottery villages across
Kyushu sponsor annual pottery fairs at which they sell their seconds and
surplus items at discounts. Most of these fairs take place during Japan's Golden
Week holidays (April 29 - May 5) when the weather is fine and people have time
to visit. Some villages also have a smaller pottery fair in the autumn, usually
for just one weekend between the end of September and the beginning of
November.
These fairs are a fantastic
opportunity to poke through the wares of multiple kilns and potters at once,
comparing, contrasting, and finding just the right souvenir. Some fairs are
better known and more crowded than others, but pottery admirers focus on the
dishes and the atmosphere created by a crowd of like-minded people. If you're
traveling from afar to attend these fairs, bring an empty wheelie suitcase to
make it easier to move around with your purchases — they can get pretty heavy!
Okawachiyama, home of
Nabeshima-yaki, hosts a fair in early April, getting a jump on the competition.
Both Hasami and Arita have fairs during Golden Week. Hasami holds its fair at
the Yakimono Park, with booths by over 100 vendors, most selling their wares at
discounts for the duration of the festival. Arita's pottery fair is Kyushu's
largest, with more than a million people descending on the village, where
nearly 500 stalls line the main street. Many studios also open themselves to
visitors during this time. Arita is one of the villages that also hosts a
smaller event in the autumn, usually around November 3.
For those interested in more
traditional earthenware pottery, Koishiwara has a three-day spring pottery fair
on May 3-5 and a fall fair on the three day weekend of Sports Day in October.
It's another chance to pick up a bargain or meet the potters at their kilns.
Karatsu also holds pottery fairs at Furusato Hall Arpino during Golden Week and
again in mid-September.
A visit to these pottery fairs and
Kyushu's pottery villages provide the opportunity to experience the ways in
which the sophisticated traditional craftsmanship of Kyushu potters has
developed and evolved over four centuries. The wide variety of ceramics produced
across Kyushu knows no bounds.